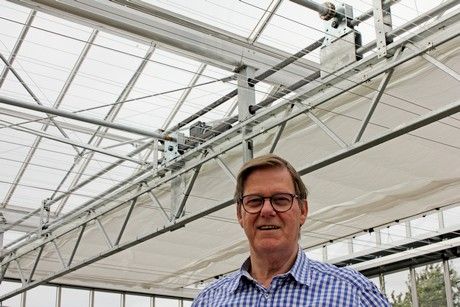
Rob Grootscholten, Bom Group
42 years of greenhouse construction in a nutshell
"In 42 years of greenhouse building, a lot has changed, but at least one thing remained the same: the Venlo greenhouse. This construction is still standing - although with quite a few upgrades - after all these years." With his retirement date looming on the calendar, Rob Grootscholten, COO BOM Group, is handing more and more tasks over to the new generation. There is always a turnover in staff, what is important we do not only hand over the knowledge, but also guarantees for the company."
From planner to operational director
Rob Grootscholten is finishing his 42nd year for the Bom Group. He started working there in June 1977, after he had finished his studies in Mechanical Engineering. After various functions, Rob became commercial director in 1998. After a management buy-out in 2001, he became a joint shareholder and since 2017 he is completely focused on the operation.
All around the church of Naaldwijk
"In the beginning, all our customers were, as a matter of speaking, located around the church of Naaldwijk. No one talked about scale enlargement. The greenhouses we built had a surface of between 1,500 and 7,500 m2. If a grower had made some money, an existing greenhouse was demolished or a piece was added."
Crisis
Rob will never forget the crisis of the 1980s. The market deflated quickly as a result of high energy costs. "We still got the order to build 22,000 m2 in Bleiswijk. That was remarkable." To save on costs, growers had to save energy, so Bom then also started to supply screen installations, and in 1983 an in-house heating department was founded. Saving energy has had a large role in greenhouse horticulture since then.
CASTA Greenhouse Construction
The calculation program CASTA Greenhouse Construction was the next step. The program was developed by TNO together with various companies from the sector. Rob: "Suddenly, we were able to calculate all profiles of trellis plants. That was awesome". This program separated the wheat from the chaff. Insurers and financiers were suddenly much better able to assess risks, and greenhouse builders did not have a kilo too much of material when starting.
Storms
That calculation of cover systems was still in its infancy became apparent in the beginning of 1990. Rob can clearly remember the storms which caused a lot of damage. "You can develop great things - extend panes and increase the height of greenhouses - but in reality, it has to be installed properly. During these storms, the mistakes in assembly were punished. The sector has learned a lot from this of course."
Large, larger, largest
More changed in greenhouse construction. Rob sums up: "First, there is the glass. With drawn glass and float glass, you had already run out of options. The drawn glass from Eastern Europe had the great advantage that it had a high light transmission. Growers back then already loved light. But the drawn glass is very fragile, and the dimensions could be better, which caused a lot of curses when installing."
In time, glass would make way for (isolated) plastic panes, the thought was. "But you can see, the glass remained, though an entire evolution with coatings followed. As of 2012, the standard became hardened glass. This glass is five times stronger, and can be used for larger sizes."
Sizing also quickly developed. "The box distances and hood widths became increasingly larger. The glass width went from 73 cm in the eighties to the 1.67 meter we now often see." The greenhouses also became higher. "In the beginning of the eighties, the height was 2.4 m to 2.7 m. Then Peet van der Burg built a greenhouse with a 3.5 m column height. When I saw the guy, I could understand why." By now, a production greenhouse with a column height of 7 meters is, especially in the lighted vegetable cultivation, pretty normal.
Everything customized
"We used to use the word 'standard'. Well, it is hardly used anymore. Each project is like a custom-made suit, fit for the location, the logistics, and everything else. The production method of greenhouses also changed. We used to have certain materials in stock, such as galvanised steel AC or APD gutters. Now, everything is tailor-made for each project, because you don't know today which system you will sell tomorrow."
Foreign adventures
The greenhouse construction knowledge was in the Netherlands, as they quickly knew abroad. In the seventies and eighties, Dutch greenhouse builders regularly ventured abroad. For Bom, the first trip was to - of all places - New Zealand. Rob: "That was kind of exciting. We had made a calculation error in the preparation, resulting in our people not having enough gutters. There they were, on the other side of the world. The found a company close by with a bending machine, which could supply the missing gutters."
From 2000 onwards, foreign projects became a fixed part of the Bom group strategy. "If we had not made that step, we probably would not have survived the crisis of 2009/2010. During this crisis period, which also affected the export, Bom made use of the opportunity to develop the export knowledge of his employees by giving training in the field of logistics and English and German language courses.
Steel gutters, who still remembers them?
Rob considers himself lucky to be part of a company that was at the start of various innovations which are exemplary of the current greenhouses. "It is in our genes. During the NTV exhibitions, people always first visited Piet Bom - what will he have thought up now?" The arrival of the aluminum gutter in 1982 is, according to Rob, the best development he has experienced. "What started as a signature during the Monday morning meeting is now an essential part in greenhouse construction. Aluminum can be extruded in many forms. You can make a hollow profile which makes them strong in all directions. The aluminum gutter was an enormous improvement with regard to open steel gutters, which we had to treat with coatings, and the cover system was attached with hooks and profiles to the gutter."
A recent project of the Bom Group is the 'Winter light greenhouse' at the WUR in Bleiswijk - still with the Venlo greenhouse construction.
From living room to project management
The deal used to be closed with the grower around the corner in the living room, perhaps while enjoying a cup of coffee. But the time of 'signing on the dotted line' is over. "Particularly in the Netherlands, long relations and knowing each other well played a role. But the grower has become an entrepreneur. The familiar nature made way for a more businesslike approach. As a representative, we used to go into the field with a measuring tape, now we get complete specifications. In international projects, this is still different, often with investors as clients, who want all care taken out of their hands by means of a complete project management. I will not deny I miss the sentiment a little bit."
Source: https://www.hortidaily.com/article/9143521/42-years-of-greenhouse-construction-in-a-nutshell/
Publicationdate: 17 September 2019
Back to all our news